Understanding Hydraulic Adapters Fittings: Enhancing Your Business Operations
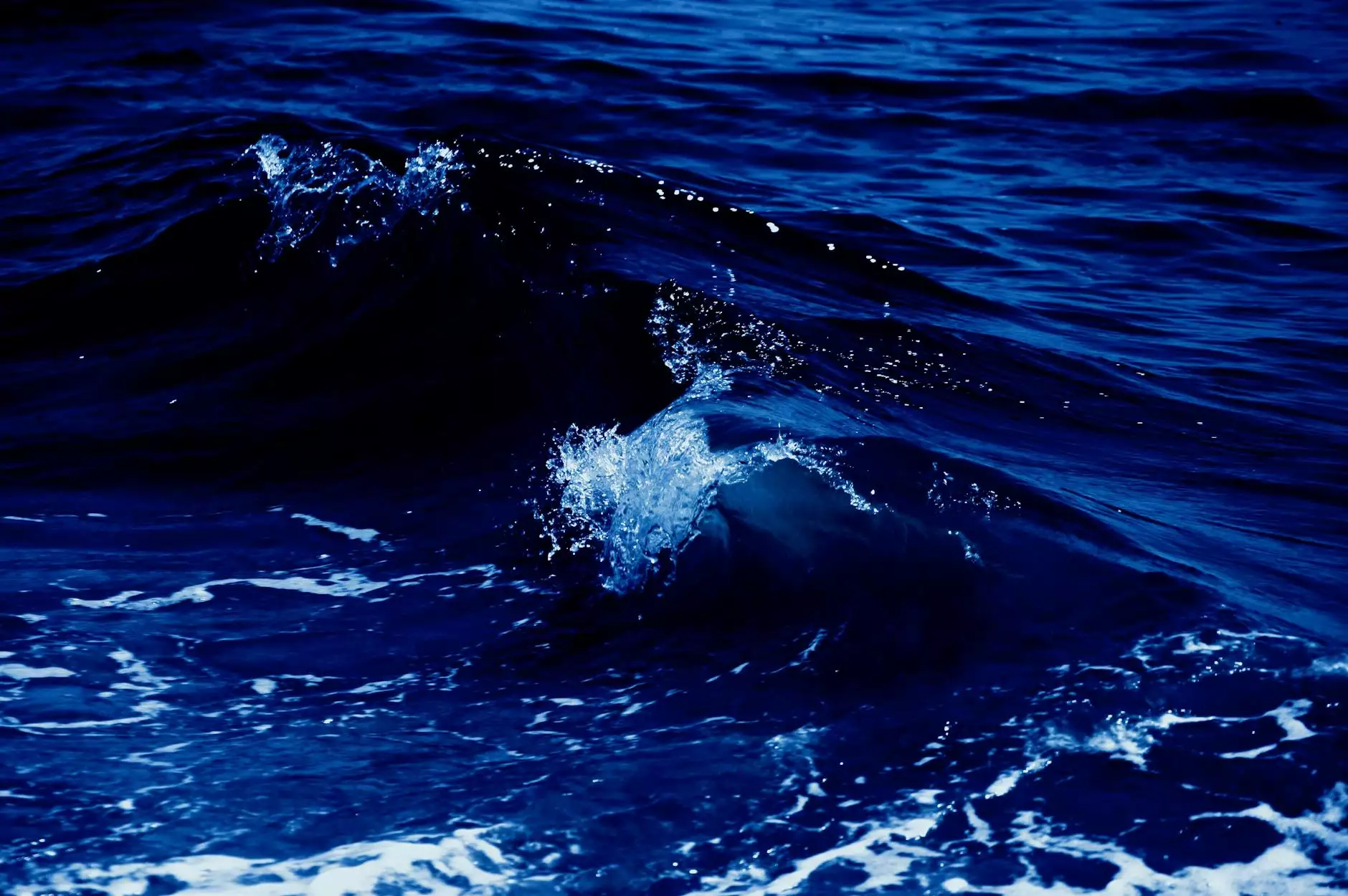
In today's rapidly evolving industrial landscape, the significance of hydraulic adapters fittings cannot be overstated. These essential components play a crucial role in the functionality and efficiency of hydraulic systems across various sectors, including manufacturing, automotive, and construction. In this article, we will explore the depths of hydraulic adapters fittings, covering their types, applications, and the best practices for selecting the right fittings for your business needs.
What Are Hydraulic Adapters Fittings?
Hydraulic adapters fittings are specialized connectors that facilitate a secure and safe connection between various hydraulic components. They are designed to handle high-pressure environments and provide a leak-proof seal, ensuring efficient transmission of hydraulic fluid. These fittings are available in several types and sizes, catering to the diverse requirements of different hydraulic systems.
Importance of Hydraulic Adapters Fittings in Business
The role of hydraulic adapters fittings extends beyond mere connectivity. Here are some key reasons why these fittings are essential in business operations:
- Efficiency: Properly functioning hydraulic systems are crucial for operational efficiency. High-quality fittings contribute to seamless fluid transfer, reducing energy losses.
- Safety: In high-pressure applications, the risk of leaks can lead to accidents. Quality hydraulic fittings enhance safety by preventing leaks and ensuring stable connections.
- Durability: Durable fittings withstand corrosive fluids and extreme pressures, reducing maintenance costs and downtime in your operations.
- Versatility: Hydraulic fittings are adaptable to various applications, making them valuable in multiple industries.
Types of Hydraulic Adapters Fittings
To effectively meet the diverse needs of various applications, hydraulic adapters fittings come in a range of styles. Understanding these types will allow businesses to choose the correct fittings for their specific needs.
1. Threaded Fittings
Threaded fittings are among the most common types used in hydraulic systems. They feature male and female threads that allow for easy and secure connections. These fittings can be made from materials such as steel, stainless steel, and brass.
2. Flange Fittings
Flange fittings are designed for high-pressure applications. They consist of a flat plate with holes for bolts, allowing for a secure connection to accommodate large volumes of fluid.
3. Quick Disconnect Fittings
Quick disconnect fittings enable rapid connections and disconnections without the need for tools. This feature is particularly useful in applications where components need frequent replacement or maintenance.
4. Push-to-Connect Fittings
Push-to-connect fittings are designed for easy installation. They allow tubing or hoses to be pushed into the fitting, creating a secure connection. These fittings are often used in low-pressure applications.
5. Barbed Fittings
Barbed fittings create a secure connection with hoses by utilizing barbs that grip the hose, ensuring a tight fit. They are commonly used in low-pressure applications and are ideal for flexible tubing.
Choosing the Right Hydraulic Adapters Fittings
Selecting the appropriate hydraulic adapters fittings is crucial for the success and safety of your hydraulic system. Here are some important factors to consider:
1. Understanding Your System Requirements
Before making a purchase, understand the specifics of your hydraulic system. Consider the pressure ratings, fluid types, and temperature ranges to ensure compatibility.
2. Material Selection
The material of the fittings affects their performance and lifespan. Opt for materials that can withstand your system's operating conditions and environment. Steel, stainless steel, and brass are widely used, each having its advantages depending on the application.
3. Size Compatibility
Ensuring the correct size is critical. Mismatched sizes can lead to leaks or system failures. Consult manufacturer's specifications and industry standards to select the appropriate sizes for your hydraulic components.
4. Quality and Certification
Invest in high-quality fittings from reputable manufacturers. Look for products that meet industry standards and certifications, which reflect their reliability and performance in your operations.
5. Application Specificity
Different applications may require specific types of fittings. For instance, high-pressure systems often necessitate flange or threaded fittings, while general-purpose uses may be served adequately by quick disconnect options.
Applications of Hydraulic Adapters Fittings
The versatility of hydraulic adapters fittings means they are widely used across numerous applications:
1. Manufacturing
In manufacturing, hydraulic systems drive machinery and tools, making reliable fittings essential for ensuring operational efficiency and minimizing downtime.
2. Construction
Construction equipment, such as excavators and bulldozers, rely on hydraulic systems for powerful operation, necessitating durable and reliable fittings that can handle extreme conditions.
3. Automotive
In the automotive sector, hydraulic systems are used in braking and steering mechanisms. Using high-quality hydraulic fittings is essential for vehicle safety and performance.
4. Agriculture
Agricultural machinery operates under demanding conditions, and quality fittings help ensure that hydraulic systems perform reliably under various operating environments.
5. Oil and Gas
In the oil and gas sector, hydraulic systems are employed in extraction and transportation. Robust hydraulic adapters fittings are crucial for preventing leaks and ensuring safety in this high-risk industry.
Benefits of Investing in Quality Hydraulic Adapters Fittings
Choosing high-quality hydraulic adapters fittings has several advantages for businesses:
- Reduced Downtime: High-quality fittings minimize the risk of leaks and failures, leading to reduced downtime and increased productivity.
- Cost Efficiency: Although the initial investment may be higher, durable fittings can lead to significant cost savings over time due to lower maintenance and replacement needs.
- Enhanced Safety: Quality fittings reduce the likelihood of hydraulic failures and accidents, promoting a safer working environment.
- Improved Performance: High-quality adapters ensure better flow characteristics and efficiency, significantly enhancing overall system performance.
Installation Tips for Hydraulic Adapters Fittings
Proper installation of hydraulic adapters fittings is crucial for optimal performance. Here are some essential tips to keep in mind:
1. Cleanliness is Key
Ensure all components are clean before installation. Dirt and debris can cause leaks and system failures.
2. Follow Manufacturer Guidelines
Always adhere to the instructions provided by the manufacturer regarding installation techniques and torque specifications.
3. Inspect Seals
Check seals and O-rings for any signs of damage or wear, replacing them as necessary to ensure a tight connection.
4. Torque Settings
Utilize a torque wrench to apply the correct torque to threaded fittings, as improper tightness can lead to failures or leaks.
5. Regular Maintenance
Regularly inspect your fittings as part of your maintenance schedule to ensure they remain in good working condition.
Conclusion
In the world of hydraulics, the importance of hydraulic adapters fittings is undeniable. These components enable systems to operate efficiently, safely, and reliably across various industries. By investing in high-quality fittings and understanding their types, applications, and installation best practices, businesses can enhance their operational efficiency and longevity. For businesses looking for reliable fittings, fitsch.cn offers a diverse range of high-quality fittings for sale, tailored to meet diverse industrial needs. The right choice of hydraulic adapters fittings can make a significant difference in your business operations, leading to productivity gains, improved safety, and long-term cost savings.